product
a product from the industrial revolution
Invented in 1856 to make hats, corrugated paper (which came before the cardboard version), had two British inventors, Healley and Allen. At first they used a simple manual machine with notches.
The first recorded use of it as packaging was in the United States in 1871, to wrap fragile objects like glass bottles. A little later, an American named Oliver Long got the idea of combining corrugated paper with cardboard to make the cardboard stronger.
From then on, the product was used more and more often, and American companies made large-scale use of it.
Corrugated cardboard has changed over the past 130 years according to the needs of its users and the market.
an innovative production process
Corrugated cardboard is essentially a kind of sandwich, with a folded layer glued to two opposing flat layers. The flutes can be anywhere from 1 mm to 8 mm apart. The average weight of corrugated cardboard is 575 g/m². The cover layers make the product strong and regulate temperature, and can be printed with information as needed. The flutes make sure the packaging stays rigid, but retain a certain amount of elasticity, making them good shock absorbers.
In order for it to be used in many different ways, corrugated cardboard can be made in different ways. The main kinds of corrugated cardboard are:
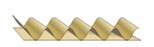
Single face:
A single covering layer with flute layer stuck on with glue.
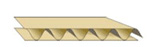
Double face or single wall:
A second covering added to the single face.
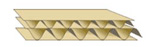
Double wall:
A second single face is added to a double face.
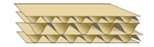
Triple wall:
Three single faces with an added cover layer.
Corrugated cardboard is made with machines called corrugators.

These very complicated machines can make up to 300 meters of corrugated cardboard per minute. They can be modified to change the size of the flutes (the folds) according to the way the corrugated cardboard will be used.
To know more about corrugated board manufacturing
a safe, hygienic product
Corrugated cardboard packaging allows for optimal transport and stocking of food products which respects current hygiene regulations:
• It’s a one-use product, making contamination risks impossible as the same packaging is not reused.
• All corrugated cardboard packaging is recycled. The recycling process subjects it to high heat, which eliminates all sources of contamination.
regulations
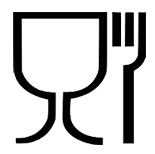
In the case of corrugated cardboard which comes into direct contact with a food product, regulations stipulate that the product not modify it in any way in order to:
• Eliminate any danger to human health,
• Avoid any inacceptable modification of the composition of the food,
• Avoid altering the organoleptic qualities of the packaged food (taste, smell).
It also stipulates that the packaging producer must respect these conditions and give their client a declaration of conformity to these regulations.
→ Here are the general regulations
→ Here are the specific paper and board regulations
→ Here are the specific coated paper and Board regulations
professional commitments
Professionals in the sector have also created guides to good practices, both in France and internationally.
This European guide, written by the CITPA and the CEPI (and validated by PIRA international, an independent organization specialized in the paper, packaging and printing sectors), aims to help companies conform to European regulations without supplanting national ones.
For more details, click here
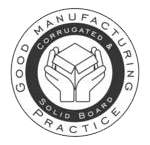
Launched at the end of 2003 by the FEFCO, these regulations guarantee corrugated cardboard passing all quality/security measures (versatility, weight, strength, and recyclability) and any hygiene measures that exist in the food industry.
For more details, click here
This French guide was created by the group on the safety of products in contact with food (MCAS), gathering together the French producers in this sector, and the national center for research and recommendations on nutrition and food (CNERNA). It was recognized by the state in 1997.
It helps producers conform to regulations and “constitutes, for the state and its official organizations, a framework and a tool enabling the respect of the rules which the sector itself defined”.
Finally, in 2002, the French food and drink industry (ANIA) and the packaging industry (CLIFE) signed a charter on all the links in the food production chain, particularly concerning packaging. It committed itself to three points:
• Making sure regulations, norms, good practice guides are respected where they apply to their activities, and to put into action any means possible to ensure the security of their products;
• Reinforce the chain of guarantee by communicating better, and ensuring the reliability of the information communicated;
• Adapting to technical progress made on food production security, on their own initiative and as quickly as possible.
Several tools have been created within this context, such as a model declaration of conformity, or a guide to client/supplier relations for the products and articles which come into contact with food products.